4 Ways Modern Construction Techniques Can Make 'Housing For All By 2022' Possible
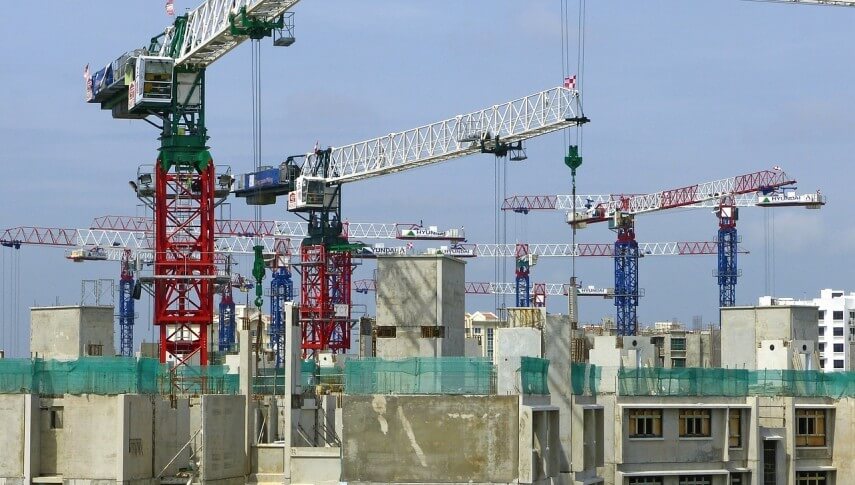
The Narendra Modi government, earlier this year, unveiled its ambitious 'Housing for All by 2022' programme to build as many as 20 million homes in India in seven years or less.
In order to achieve this country-wide project, there is need of skilled workers such as plumbers, electricians, and masons in remote areas, where the government plans to provide affordable homes. Faster construction timelines coupled with better utilisation of space, including lowered construction cost, in order to deliver affordable homes to the public. This can be achieved by using modern construction techniques.
Let's look at some of the benefits of modern construction techniques:
- Cost lowering: The 'Housing for All by 2022' scheme includes rehabilitation of slum dwellers. Real estate developers who will be looking at lower margins from low-cost homes, will have to look for ways to maximise it. The use of prefabricated construction material, which though cost higher than the traditional method, save time and money in terms of transportation and labour. The time taken for construction reduces by at least 15 per cent, when prefabricated materials are used. This can further lead to savings on interest costs as well as long-term savings in the form of reduced storage space of construction material. It will also cut down cost of pilferage and wastage of construction materials such as cement, mortar and brick, cutting down on incidentals.
- Labour worries: Though labour is aplenty in India, the construction sector has been having troubles of skilled manpower. Moreover, there is a need for expert electricians and plumbers; need for skilled labour in fast-developing areas, which have multiple under-construction projects; and the inability to hire skilled labour in remote areas. This has led to extra costs for the developers who recruit and relocate labourers, leading to mini-slums around the under-construction properties. Modern technologies such as prefabricated materials ensure right kind of experts are used to manufacture slabs, kitchen units, and bathroom modules, which can be later assembled at the site. These materials are also pre-equipped with plumbing and electrical work. Thus, ensuring that the site need not hire many experts. The cost of labour for modern construction technologies is over 30 per cent, more than making up for higher material cost.
- Quick turnaround time: The biggest advantage of using modern techniques ensures that turnaround time is very high, especially when constructing high-rise projects in India. The use of jump form technology can help build large structures in a few months. Most of the equipment used in modern construction are imported. However, many developers say that these machines more than make up for the customs duties, and hiring/purchase cost of the equipment. Faster turnaround time will ensure that developers would have fewer liquidity problems, with shorter time-to-market.
Affordable residential projects have to be completed in a timeline of around 18-24 months, which is possible only when modern technologies are applied.
- Quality of construction: It can be tough to meet specifications of a building by developers as it is directly proportional to the kind of expertise such as foremen in an area. This has led to many developers hiring and relocating a number of workers inching up costs and time taken. But prefabricated materials are built at factories with pre-defined specifications and under strict supervision, before being shipped off to the site, thereby ensuring the quality of construction.
(Katya Naidu has been working as a business journalist for the last nine years, and has covered beats across banking, pharma, healthcare, telecom, technology, power, infrastructure, shipping and commodities)